Today, more than ever, modern societies depend on technology and machines. We travel in cars, buses and trains, relying on the turbines of aeroplanes and power grids. It's easy to forget how much our life depends on machines – until they happen to fail. Care, maintenance and servicing are crucial. While companies rely on a certain amount of planned downtime to inspect machines for safety and necessary repairs, unplanned downtimes and sudden trouble can lead to enormous losses. They upend production plans, bring considerable costs, and result in a loss of customer confidence. Developing and implementing suitable maintenance strategies is more important than ever – and the trend here is towards proactive maintenance.
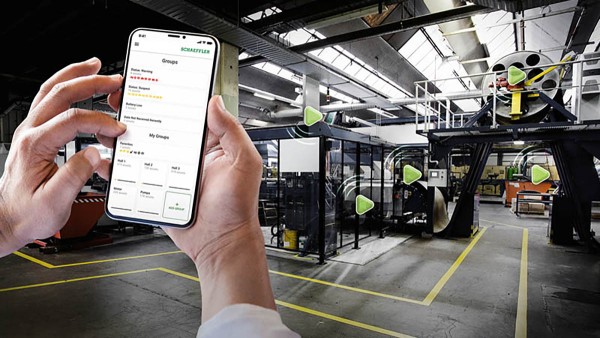
Condition monitoring is a proactive tool: Sensors monitor units or individual components directly at the machine by measuring temperatures, rotational speeds, or vibrations. Algorithms analyse the data in real-time and provide information about wear. This shortens or even prevents downtime, produces less scrap and reduces maintenance costs. In the industrial world, the cost and effort involved in integrating such solutions into production environments is often a hurdle to machine monitoring.
Setting up and operating these solutions requires in-depth know-how—coupled with the costs incurred, which can scare off small and medium-sized enterprises from investing. As a result, condition monitoring is limited primarily to individual process critical machines.
"In the process and automation industry, it's not uncommon for up to 95 per cent of equipment units to not be monitored at all, or only through routine manual measurements, which occur at intervals of four to six months, for instance," says Rauli Hantikainen, Senior Vice President of Schaeffler Lifetime Solutions. In Germany alone, several million so-called brownfield machines lacking sensors and software interfaces are in operation. However, this doesn't have to be a showstopper.
Long-established Polish company Albeco, which specialises in the sale of bearings and linear products, had expanded its maintenance management division—faced with the challenge of finding a conditioning monitoring solution that monitored many machines involved in complex production processes minimised on-site visits to customer sites.
Albeco reached out to Schaeffler, who recommended their OPTIME monitoring system, an easy-to-use condition monitoring solution in an attractively priced segment. The OPTIME solution proved to be a successful solution, with numerous customers from various industries enthused by the outlay associated with the installation. Jakub Burdajewicz, expert for Condition Monitoring at Albeco shared his thoughts "With Industry 4.0 solutions from Schaeffler (now Schaeffler Lifetime Solutions). We can serve our customers better and ensure less downtime. This opens new business areas for us as a service provider. Our customers are satisfied. And naturally, so are we".
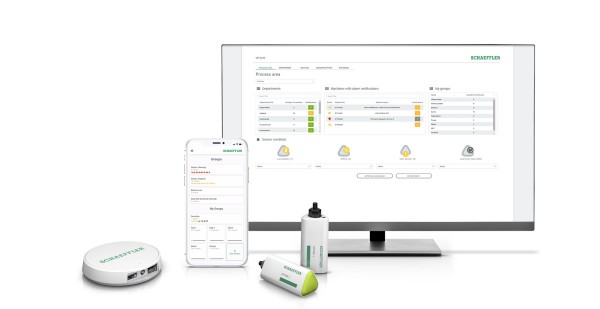
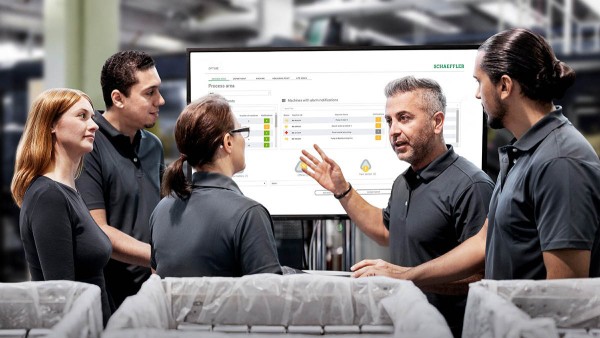
Whereas monitoring solutions for process-critical machines with variable operating conditions may cost tens – or even hundreds– of thousands of euros, OPTIME monitors at 30 per cent of the cost compared to route-based, or online measurement systems, making it economical even for smaller drive units and motors. Unplanned downtimes can be reliably avoided as Schaeffler's OPTIME keeps an eye on many of your machines.
For companies operating in system-intensive processes, avoiding unplanned downtimes means greater profitability. Via the smartphone or desktop app, OPTIME customers constantly watch their plant's status, even with hundreds of machines, as the messages are user-friendly and prioritised according to criticality. As a result, in-house maintenance personnel or service companies can plan maintenance measures, personnel utilisation, and the procurement of replacement parts in a timely and cost-efficient manner.