Design your cobots without any compromises
Choosing the right system components for cobots and lightweight robots can improve their performance, while providing cost advantages and greater design freedom, says Ralf Moseberg, Head of the Industrial Automation Business Unit at Schaeffler. With this in mind we took the time to probe Mr Moseberg further on the challenges and how Schaeffler supports in the design of cobots.
What challenges are cobot and LWR manufacturers facing in particular and what are their primary goals?
In the manufacturing industry, there is a desire to use lightweight robots (LWRs) and collaborative robots (cobots) much more flexibly, as well as "small industrial robots" in a highly productive manner. The main aim of robot manufacturers is to open up further industries and fields of application for their products. The projected unit sales are massive.
What advantages do Schaeffler components offer cobot manufacturers?
The outstanding advantage for our customers is not merely the ability to improve certain performance data, such as the payloads or the speeds. With our components, they have the freedom to choose the percentage they increase the speed and decrease the positioning time and, for example, allowing a higher motor temperature as the motor-gearbox design allows it. The cobot designer is free to move conceptually on a wide playing field and has to make few, if any, compromises. This freedom will enable manufacturers to adapt their LWRs and cobots much better to specific "ranges of tasks" in industrial production.
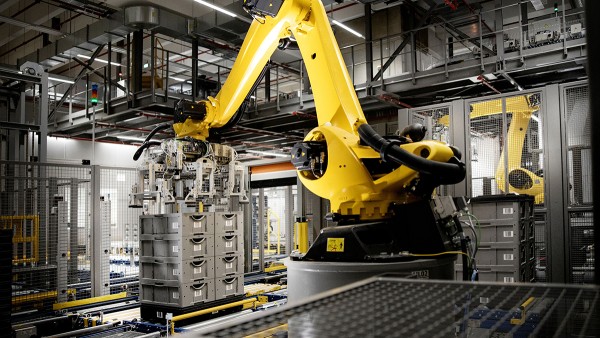
What do you mean by "ranges of tasks"?
Imagine a lightweight robot is to be developed for assembly purposes in highly automated manufacturing environments, with a payload of ‘x’ kg, high duty cycle, high number of cycles but also with the ability for occasional collaboration. This requires a drive with particularly low power dissipation and good heat dissipation, as well as a very rigid cobot structure. This in turn requires correspondingly tilt-resistant bearings and torsionally-stiff gears. If at all possible, the sensor system should not influence the positioning accuracy.
Another example: the task is to develop a cobot for a high proportion of third-hand operations. This can only be achieved with low power dissipation and very low cogging of the motor as well as a precise torque measurement system. We provide the necessary advances in all these disciplines.
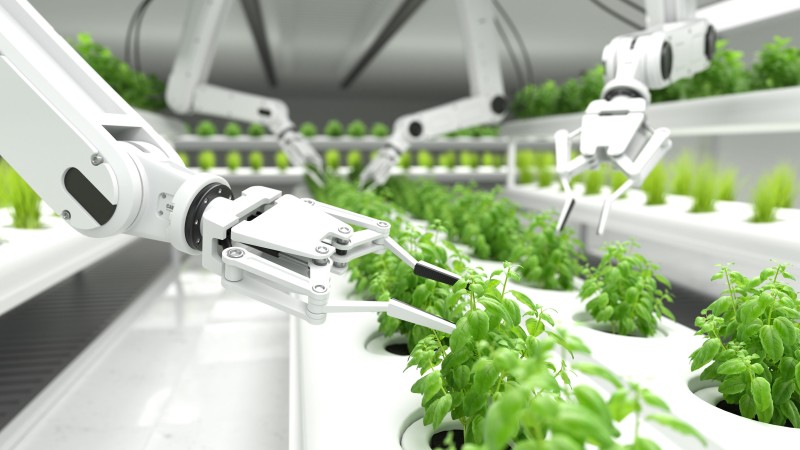
Schaeffler solves the problem of measuring external loads with an integrated torque sensor system. What is special about it and what problems does it solve?
The attractive aspect of sensors integrated in each axis is basically that you know the precise torque in each axis and incidentally also the torsion angle of the individual arms from the stiffness characteristic of the gears. In terms of control technology, it is now possible to compensate for this deviation and therefore improve the positioning accuracy under load.
Our sensor technology is an integrated part of the gearbox, so it requires no additional installation space and adds hardly any weight. Most importantly, the sensor technology does not affect the rigidity of the gearbox or the precision of the robot, as is commonly the case with many other solutions on the market. The sensor system supports the safety functions as well as the positioning and process feedback control and can also be used for implementing active vibration compensation. This allows the natural vibration behaviour of the small robots to be controlled at high accelerations and the positioning time to be further reduced.
Do the sensorised precision gear units also offer cost advantages?
The return on investment (ROI) is the metric by which nearly every economisation measure and every automation solution is evaluated. The ROI is mainly determined by the life and the cost of the overall solution. With respect to cost, the sensor solution provides a decisive advantage – having 6-axis force torque sensors and sensors screwed into each joint proves to be too expensive for many applications. In contrast, the torque sensor system of Schaeffler’s RT1-T precision strain wave gear series is extremely economical because no additional (elastic) sensor element is required and the sensor does not have to be installed in the articulated arm as a separate component.

You can find more information on products and solutions for the robotics industry here: Industrial Automation: Robotics