Food for thought
Downtime can be disastrous for food and beverage processing companies and the consequences of interrupted production are enough to give even the most hardened plant manager sleepless nights. With competition more intense than ever and margins under unprecedented pressure, manufacturers can end up losing significant sums of money through machines sitting idle and product not going out the door and generating revenue. Put simply, for today’s manufacturers minimising downtime is as pivotal as maximising quality and output.
Monitor and manage
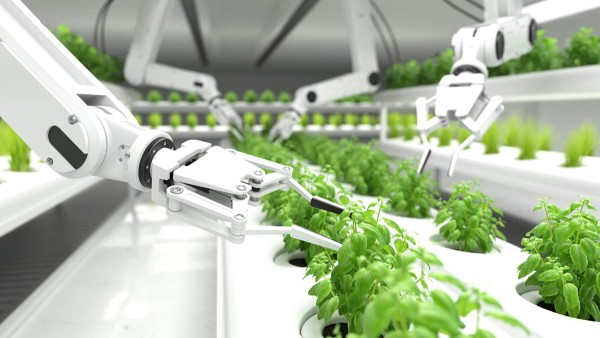
A 2016 study by Aberdeen Strategy & Research put the cost of unplanned downtime at $260,000 (£230,000) per hour, so in order to address this issue the industry has started exploring the advantages of Industry 4.0, or Lifetime Solutions in Schaeffler language, to improve matters. Some leading manufacturers have realised that by adopting cloud based solutions they can gain great benefits at both monetary and operational levels.
A typical processing plant comprises an array of complex and highly sensitive equipment across the production line. Manufacturers cannot afford to wait until a piece of machinery breaks down completely, leading to contamination, wastage and lost production time – they need to know the condition of their plant at all times.
Condition based maintenance solutions such as Schaeffler's pioneering OPTIME use easy to fit sensors to assess criteria including vibration and heat. The data collected can establish trends, predict failure, assess degradation. As a result, maintenance is only carried out when a consistent decrease in machine condition is identified, creating value through asset optimisation and lowering total cost of ownership.
Moving on up
The potential of condition based maintenance is developing all the time. For example, when it comes to machine failure lubrication is a major issue that plagues food and beverage production facilities, with agents that deteriorate lubricants, resulting in corrosion. A survey by Machinery Lubrication revealed that 80 percent of reliability engineers reported instances of equipment failures from lubrication starvation, so a proactive approach to maintenance is the most effective strategy.
Condition based maintenance systems can provide key information on all networked lubricators, similar to Schaeffler's smart lubricator OPTIME C1, ensuring optimal lubrication of machine components and preventing the formation of wear particles. Effective lubrication can also help protect machines from the aggressive cleaning agents used in washdowns, which can lead to downtime.
Selection procedure
The reliability of components plays a key role in minimising total cost of ownership (TCO), maximising operational efficiency, achieving regulatory compliance and enhancing employee safety. Within food and beverage processing environments, more than ever this is the case with rolling bearings.
When it comes to effective maintenance, repair and operations (MRO) activity, longer service life is vital and only rolling bearings that are able to continuously withstand moisture and extreme temperatures can ensure dependable operation. The demands placed on this equipment present a real challenge and the operating condition of rolling bearings can be affected by high temperatures, high speeds and exposure to water.
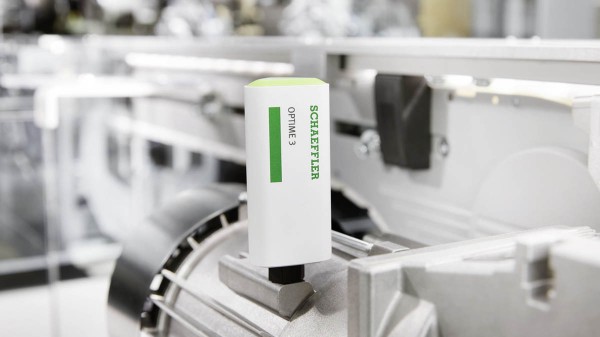
Two-way street
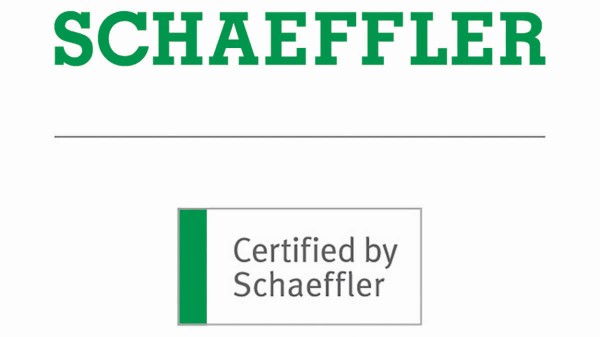
Using rolling bearings from reputable manufacturers such as Schaeffler and purchased through its certified and trusted distribution partners, can play a vital role in ensuring machine longevity. Far from being the ‘middle men’, distributors are the customer facing experts, while manufacturers are focused on designing, developing and producing products that meet the needs of end users.
Distributors are also in an excellent position to provide advice about rolling bearing specification, utilising technical support from manufacturers such as Schaeffler. Through its INA and FAG brands, Schaeffler has the widest product portfolio in the rolling bearing industry and the X-life range is characterised by longer life – the result of higher dynamic load ratings – which makes it the perfect choice for much of the machinery in food and beverage processing environments.
Keep on running
The food and beverage production industry has many unique challenges. Every machine in a production line needs constant monitoring and attention, which is a particular challenge in environments that operate on a 24/7 basis. The reliability of components therefore plays a key role in minimising TCO, maximising operational efficiency, achieving regulatory compliance and enhancing worker safety.