Firing on 4 cylinders
Industry 4.0 has now evolved to a stage where it is possible to gather and analyse data across machines, enabling faster, flexible and more efficient processes that can produce high quality goods at reduced costs. However, some organisations are still failing to recognise the benefits that condition based maintenance (CBM) offers and how it can maximise the potential of this new industrial age.
Industry 4.0 – so named because it is considered the fourth industrial revolution – is not new. The term was originally coined by the German Federal Ministry of Education and Research (BMBF) to refer to the digitisation of the manufacturing industry. At the Hannover Messe Industrie (HMI Fair) in 2011, the BMBF demonstrated how cyber-physical systems could be responsible for the evolution of new manufacturing and industrial automation models.
Disruptive influence
Now, the disruptive pace of Industry 4.0 is being felt across every sector and entire industries have been transformed in the space of a few short years by digital transformation-based technologies. The global market for Industry 4.0, which was estimated to be worth $90.6bn in 2020, is projected to reach $219.8bn by 2026, growing at a CAGR of 16.5 per cent over the analysis period.
Manufacturing plants all over the world are adding a digital element to existing automated assembly line structures, allowing machinery and plant to communicate. Firms embracing this new style of manufacturing are experiencing increased efficiency, automation, agility, security and resilience as a result.
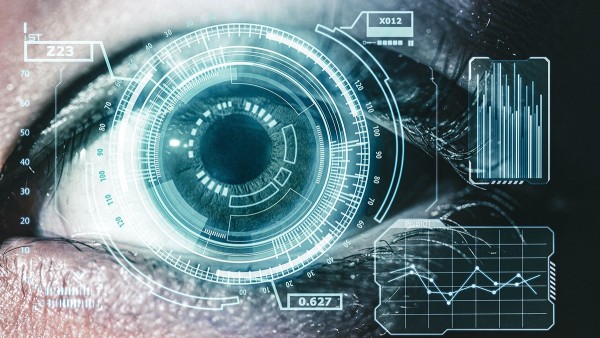
Knowledge is power
One of the key drivers of Industry 4.0 is the desire to have machines operating with as much autonomy as possible, with the ability to spot potential problems and identify possible solutions at the earliest opportunity, before they are noticed by an individual. However, although it can optimise production, shorten time to market and enhance flexibility and responsiveness, many manufacturers are still failing to fully acknowledge the role that condition based maintenance plays in underpinning an entire Industry 4.0 infrastructure.
As one of the most effective ways to ensure equipment uptime, all too often it is often only used on critical machinery due to high implementation costs. However, by adding intelligence to sensors it is now possible to monitor and assess the performance, quality, efficiency and status of machinery in ways that are both cost effective and readily available.
Condition monitoring uses sensors to measure the status of a piece of equipment while it is in operation. The data collected can be used to establish trends, predict failure, assess degradation and calculate remaining life. As a result, maintenance is only carried out when a consistent decrease in performance is identified, creating value through comprehensive asset optimisation. Schaeffler's OPTIME is leading the way in this area, making it possible to configure condition monitoring that can detect potential damage, vibration, imbalances, knocking and/or misalignments in a gearbox or drivetrain, for example, before serious problems occur.
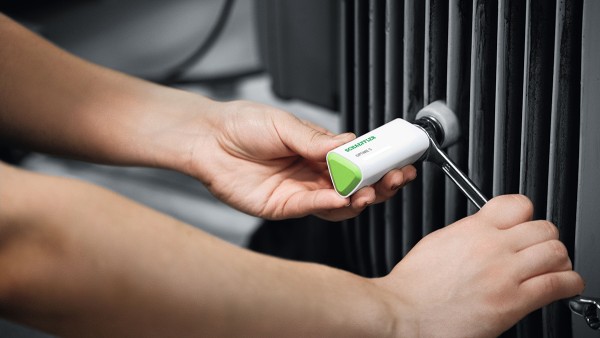
That this system is affordable and easy to implement means that condition monitoring can be applied to smaller pieces of equipment, not just critical pieces of the plant where failure would prove highly disruptive. Even smaller gears, drives and other non-critical components can bring activity to a halt when they fail. As a result many organisations operate a planned ‘swap out’ of these pieces of equipment to counteract any potential failure. This is a costly and wasteful exercise and one that is entirely unnecessary if condition monitoring is adopted on these types of machinery.
Remote control
One of the surprising knock-on effects of the coronavirus pandemic is the way in which it is triggering a powerful acceleration of innovation in manufacturing. Management consultant McKinsey believes that the last several months have seen more progress than would otherwise have been seen in years at the previous pace, while Amar Hanspal of manufacturing software firm Bright Machines believes that Covid-19 has ‘shone a light on the importance and value of digitising and automating factory operations’.
This, in turn, is already having a direct effect on the uptake of condition based maintenance. In light of recent lockdowns, social distancing, furloughing and travel restrictions, the ability to remotely monitor manufacturing equipment has become vital in ensuring that any issues are recognised quickly, and any remedial action taken. It is possible for designated personnel to receive clear statements about the real time condition of machines via the Schaeffler mobile app from wherever they happen to be.
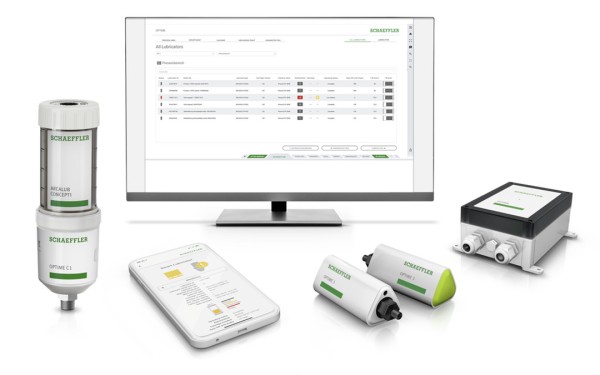
The potential of condition-based maintenance is therefore developing all the time. For example, when it comes to machine failure, lubrication is a major issue – equipment may either be over-lubricated, under-lubricated, lubricated when a machine isn’t operational, or given the wrong type of lubricant. Indeed, 80 per cent of premature rolling bearing failures could be prevented through the use of proper lubrication - and this is why Schaeffler's OPTIME C1 has been developed to provide maintenance crews with key information on all networked lubricators, enabling targeted maintenance of relubrication systems and eliminating the need for manual, route-based checks. The next step is to introduce a condition-based system where machines are kept optimally lubricated at all times.
The times are changing
Condition-based maintenance should be at the heart of an Industry 4.0 strategy. Whether a facility is involved with raw material extraction and processing, mining, paper production and pulping, food and beverage manufacture or cement production, the amount of data that can now be generated is exponential and enables manufacturers to make well informed business decisions, save money and improve their production efficiency.