Embrace automation and elevate productivity
Industrial automation (IA) is no longer a nice-to-have, but a necessity. Richmond Averill, Industrial Automation OEMs, UK and Ireland at Schaeffler UK, discusses how emerging trends in IA are impacting Schaeffler and its OEM customers in terms of reskilling of labour, and how robots can boost accuracy and productivity.
As industrial automation technologies continue to expand across the manufacturing landscape, businesses need to stay ahead of the curve, keep up with technological advancements and retrain their labour to adapt to these changes. Companies will still need their workforce, though their skill sets will need to be more diverse, agile and adaptable. This will require investing in reskilling, with training focussed on interdisciplinary and digital skills, automation, data analysis and blending traditional manufacturing knowledge with digital automation expertise.
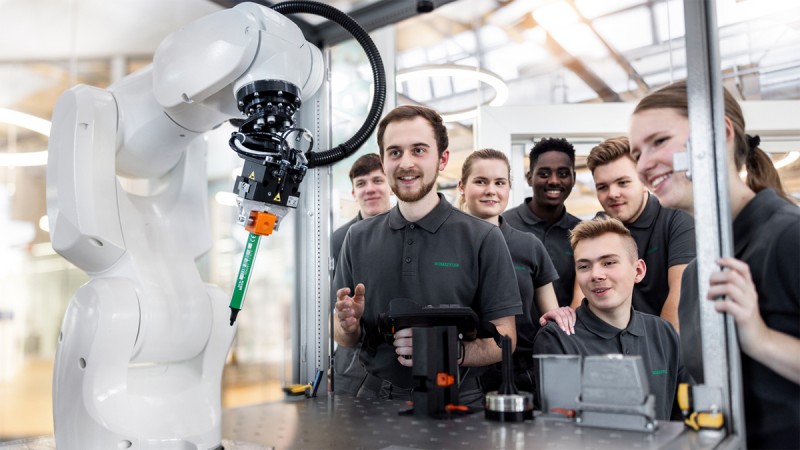
As a manufacturing business, Schaeffler is integrating automation technologies alongside its existing workforce. Workers without advanced technical automation skills are being encouraged to retrain to ensure they can readily adopt and adapt to these transformative technologies. With automation and humans working alongside each other, manufacturers will be more resilient to ongoing labour and skills shortages, allowing them to increase production and efficiencies.
In the UK, most of Schaeffler’s customers are OEMs, machine builders or systems integrators. We work closely with the developers and designers of machines that are sold to a wide variety of industry sectors to help manufacturing end users automate their own production processes. The OEMs have integrated some automation technologies within their own plants, though our focus is on helping their designers develop more reliable, energy efficient machines using our products and services.
The human touch of automation
An industry which is benefiting from automation is the medical community. Machine builders are producing surgical robots which would perform an operation alongside the surgeon, through the use of a joypad controller. The robot is able to perform minimally invasive, more precise surgery on patients.
In the U.S., for example, approximately three out of four prostate cancer surgeries are now performed using automated surgery. There are now more than a hundred robots spread geographically across the UK, which is helping to free up more hospital beds, as the surgery is less invasive and the productivity of the surgeon improves so more operations can be performed. You still need the human intervention and knowledge of the surgeon, though with the robot they can be more precise, so the skills of the surgeon are actually enhanced, not replaced. It’s also safer for patients and the surgeon has more control by changing the speed of the precision motors and drives.
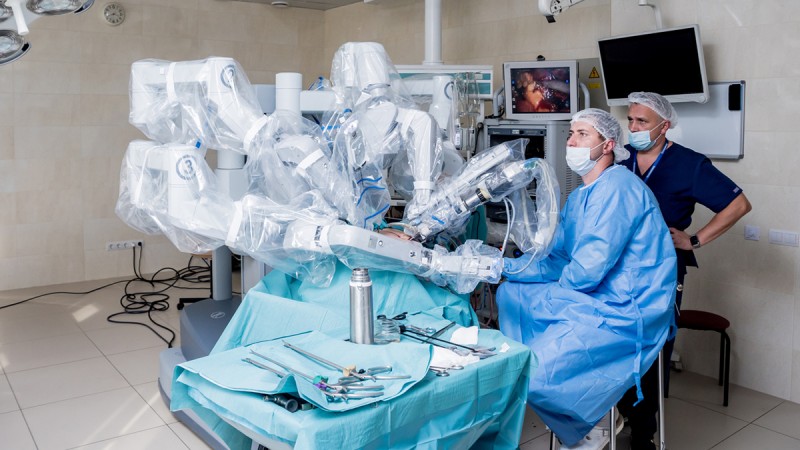
It’s happening
Automation is happening everywhere and in every sector of our economy. This can happen in the smallest of ways with a big impact. We are selling more and more sensor-based solutions, where we integrate our bearings with a sensor(s) in a single compact unit. This makes the machine more reliable and improves the quality of what the machine produces. We are supplying them with products and solutions that give them an additional layer towards automation.
Automation drives reshoring
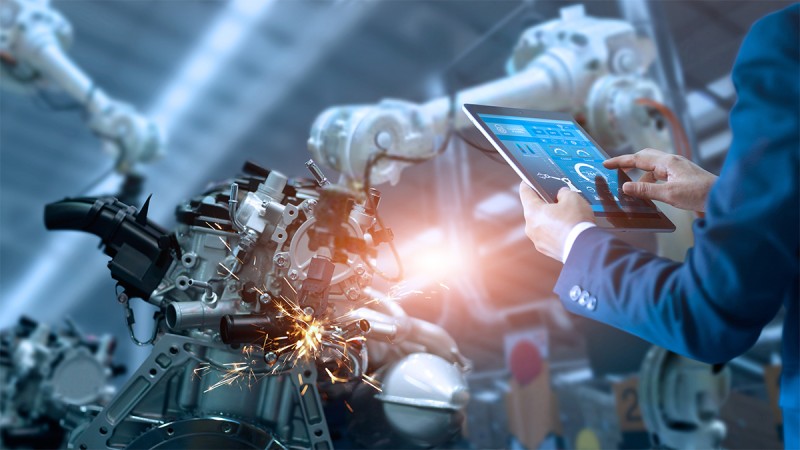
We are seeing more of our customers reshoring. Rather than moving production to countries with cheaper labour, UK-based companies are seeing more opportunities to automate. In effect, the automation becomes the cost-effective labour, which means manufacturers can produce back in the UK. The benefits include faster deliveries, more agile local supply chains, as well as being more carbon-neutral.
With consumer tastes and fashions changing at increasingly faster rates, new products must go to market quicker than ever. Speed to automation will therefore become a crucial differentiator. Our machine building customers need to develop machines that can adapt and change what they make at the touch of a button. They must adapt to changes in fashion and to products with shorter lifecycles.
By automating manual, mundane, repetitive and dangerous tasks, companies can protect their production lines from the impact of high labour turnover. By introducing robots, cobots and other automation technologies, companies will benefit from fewer sickness days, safer workplaces, higher precision production and assembly processes, higher repeatability and more layers of inspection to ensure higher quality products.
The manufacturing industry must invest more in automation technologies to become more agile, more productive and more energy efficient. In parallel, they need to invest in reskilling their workforce to ensure they can adapt to this changing landscape. Automation is inevitable, and beneficial not only to a bottom line, but the economy as a whole.
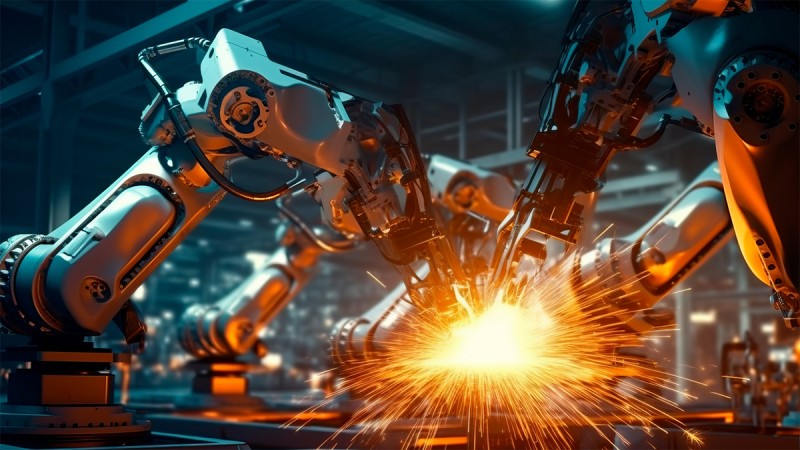