Investing in Skills
A look around the automotive industry is an indication of how fast the world is changing. Schaeffler is at the centre of these changes: since we created a dedicated e-mobility division four years ago, the number of battery electric vehicles on the UK’s roads has grown hugely, for example, by 74% between 2020 and 2021 alone. There are now some 780,000 plug-in vehicles on the UK’s roads and the infrastructure required to support these vehicles has also grown: the number of public charging points in the UK increased by 33% between March 2021 and March 2022.
Digitalisation creates opportunity
The skills required by an industry that is experiencing this great transformation are different to those required latterly. E-mobility brings greater digitisation, not only of the vehicles themselves, but also production methods and servicing. It’s important, therefore, that the automotive sector attracts people with necessary skills to advance e-mobility and hasten the sustainability that it makes possible.
A balance must be stuck, however, and a hybrid mix of skills will be needed as we move forward. While Schaeffler provides training for employees on new technologies and the particular production skills that come with this, there remains a healthy aftermarket in the UK, and ICE vehicles are going to be around for a while still. Those cars will continue to need parts and repairs, so we must ensure that our workforce has the knowledge and understanding to work in both worlds.
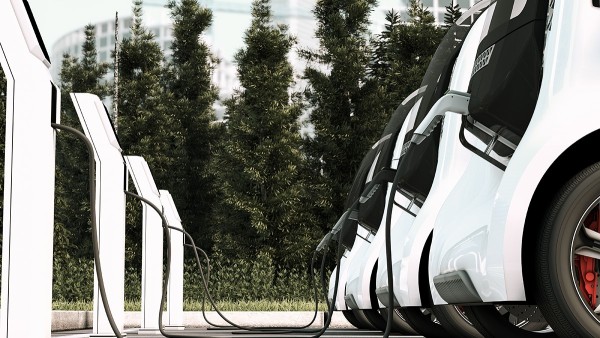
Other trends are transforming the world of work, and these also reinforce the need for the right skills sets. The pandemic and the subsequent spread of digitisation has provided more opportunities for mobile and remote working and this, in turn, has further intensified the competition for talent because opportunities have now opened up to employees that were previously inconceivable.
Inside the factory of tomorrow
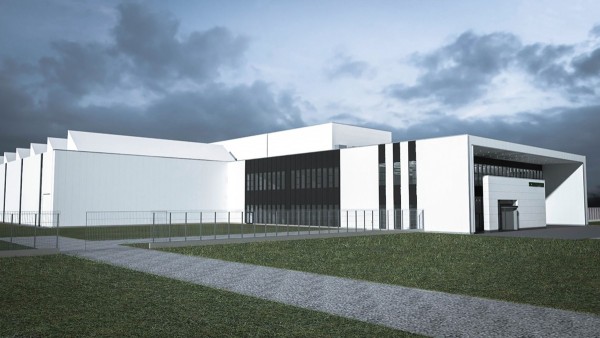
In addition, production is becoming more automated, efficient and sustainable. The factory of the future is becoming a clearer picture: Our e-mobility plant in Szombathely, opened in September 2021 not only features a high degree of automation and modular production buildings, but is digitized throughout.
Automated production lines and extensive use of industrial robots guarantee the clean, dust-free environment required by sensitive production processes used for assemblies, such as stators and rotors, and the integration of magnets for synchronous and asynchronous motors.
Our aim is to ensure our plants are all boasting the factory of the future necessities by 2040 - incidentally, the same year that Schaeffler has promised to be climate neutral. This means we need to invest in our current skilled staff to ensure that they can adapt to the developments required.
Diversity promotes innovation
Indeed, it’s not just about attracting the right people to work in a sector undergoing rapid transformation. At Schaeffler, we also invest heavily in the ongoing training of our people, whether digital, face to face, or a combination of the two. This ensures that all our employees have the skills and the knowledge to develop and grow within their roles.
Key to building a productive and skilled workforce is diversity. As a global company, Schaeffler is committed to gender equality and equal opportunities. A genuine culture of diversity and inclusion allows organisations to draw on a wider range of experiences, expertise and skills in order to better address a diverse range of customer needs.

At Schaeffler we believe that a proactive diversity and inclusion policy will meet the demands of a new generation for whom inclusion isn’t a ‘nice to have’, but an essential part of the workplace. By adopting these principles, industry can overcome the skills shortage and equip their organisations with the skilled and motivated people on which their success depends.