AR you ready for a reality check?
Why increase your global footprint by flying around the globe when a project can be managed from a desk, at home or in the office using a high-tech headset? Augmented reality (AR) plays an important role in the Schaeffler world. The technology makes maintenance processes more efficient and can enhance quality.
76.7 million professional VR headsets are expected to be sold worldwide in 2024, ten times as many as in 2020. The virtual reality market is expected to grow by 30% per year between 2022 and 2024, with the augmented and mixed reality markets by up to 57% (Forecast: Deloitte; source: marketing-boerse.de)
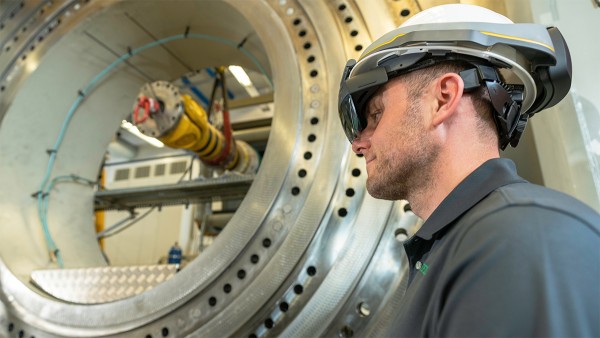
The replacement of highly stressed rolling bearings is more or less routine business in many large-scale systems. That also applies to customers of Schaeffler’s Industrial division that are at home around the world. If a bearing had to be replaced in the engine room of a large container ship in the Indian Ocean or perhaps in the London Eye Ferris wheel, support from Schaeffler’s maintenance specialists – most of whom are based in Germany – might be required. That would typically entail long-distance travel.
In order to provide help faster and more directly, the mounting experts, in addition to on-site support, have increasingly been relying on augmented reality (AR) since 2021. They set up a virtual on-site scenario by means of data glasses and computers. For remote support in real time, customers can borrow a HoloLens AR headset. A connected Schaeffler fitter guides the local worker in performing the installation on the object via a secure data connection. In inverse data flow direction, the Schaeffler employees can virtually mark a component to be worked on in the AR headset of the local fitter via depth sensors. This information remains active for a longer period of time so that no step will be overlooked. Likewise, drawings or explanatory videos can be inserted.
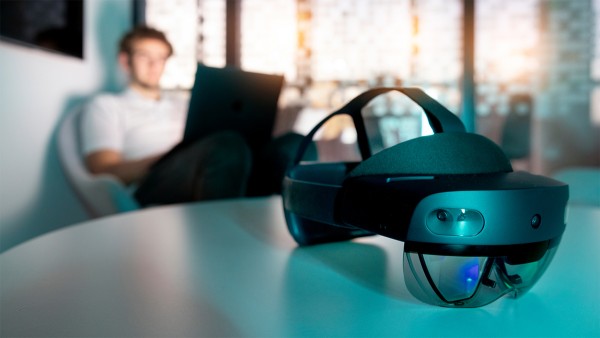
Fitting error rate drops

Schaeffler’s Virtual Fitter program offers a range of benefits: less downtime during maintenance and increased productivity. If no external personnel need to travel to the site, customers save on expenses and the carbon footprint is reduced. Even in more challenging conditions such as those during the Covid crisis, mounting jobs can be reliably accomplished. During acceptance processes, the technicians can respond faster and more precisely, and the fitting error rate drops. Personnel can be scheduled with greater flexibility because even people with lesser experience can be guided in the virtual world.
Additional benefits include faster response times in the event of problems, transfer of mounting-related knowledge to the customer, and reliable ‘hands-free’ collaboration. Where necessary, Schaeffler provides speciality tools on loan. When less-skilled workers can be instructed via HoloLens, the technology counteracts the shortage of specialists.
Schaeffler also demonstrably saves money by using AR. Reinhold Daft, Head of Mounting Services at Schaeffler, identifies 50% cost savings due to the Virtual Fitter, which now can be used in the areas of raw materials, paper production, rail, and marine sectors, as well as in wind farms and large-scale manufacturing plants. However, to customers that still prefer on-site support, Schaeffler continues to offer traditional bearing mounting and dismounting services – a perfect way to retain customers.
Investing in AR at Sheffield
The Schaeffler UK production plant in Sheffield is also seeing benefits from the use of AR. The plant used AR primarily to obtain opinions from experts at other Schaeffler plants around the world on its production lines and to help with process improvements, cost savings and machine repairs. From this learning, the plant has expanded its use by overlaying the AR with digital features. When investments are planned at Sheffield, AR has proved to be excellent for smart factory layouts and new machines. It has also helped to get people from the shop floor involved and get their buy-in on new equipment or assembly lines.
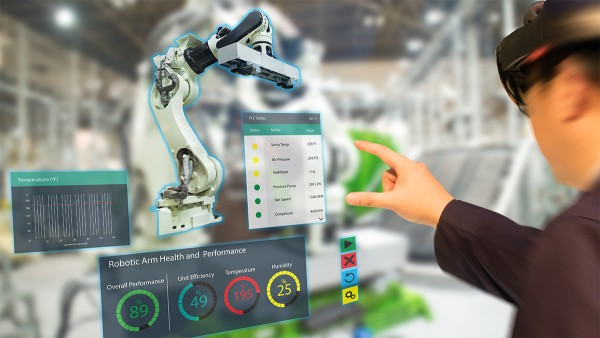
As Kevin Robson, Segment Leader Operations & Assembly at the Schaeffler UK plant in Sheffield comments: “AR is an excellent tool for sharing your thoughts and suggestions with colleagues. You can pin a display to a machine or mark-up areas on a robot, as well as show colleagues where conveyors and other ancillary equipment are located. We’ve even used HoloLens AR to show our robot cells to external suppliers, who can then suggest appropriate products to use on our machines. AR allows you to better plan projects because you can anticipate things before you actually implement them, which means you don’t have to add extra unforeseen costs at the end of the project – you can budget more accurately.”